Raise Your Requirements with Professional Welding Inspection Milwaukee Solutions
Raise Your Requirements with Professional Welding Inspection Milwaukee Solutions
Blog Article
Key Factors to Think About in Welding Assessment for Quality Control
Welding evaluation is a critical element of top quality guarantee that encompasses different variables important for making sure the stability of welded frameworks. The interplay of these elements elevates further concerns regarding just how they can be maximized to enhance overall welding high quality.
Kinds of Welding Procedures
Welding procedures incorporate a variety of techniques utilized to join materials, mostly steels, via the application of warmth, stress, or both. The most common types of welding processes include arc welding, gas welding, resistance welding, and solid-state welding.
Arc welding, that includes methods like Shielded Metal Arc Welding (SMAW) and Gas Tungsten Arc Welding (GTAW), employs an electric arc to generate heat for melting the base metals and filler materials. Gas welding, frequently referred to as oxy-fuel welding, utilizes a fire generated by shedding a fuel gas with oxygen to thaw the steels.
Resistance welding, including area and seam welding, relies upon the heat generated from electrical resistance to bond products, commonly made use of in auto production. Solid-state welding procedures, such as friction welding and ultrasonic welding, join materials without thawing them, making use of mechanical stress and frictional warm.
Each welding process has specific applications, toughness, and constraints, making the choice of the suitable technique crucial for attaining wanted weld high quality and performance. Welding Inspection Milwaukee. Understanding these procedures is necessary for making sure efficient welding practices and sustaining quality control in manufacture and production industries
Inspection Devices and methods
To guarantee the honesty and dependability of welded joints, different evaluation strategies and devices are used throughout the welding procedure. These strategies can be generally classified right into non-destructive testing (NDT) and destructive screening (DT) methods. NDT approaches, which do not compromise the honesty of the welded part, include aesthetic inspection, ultrasonic screening, radiographic testing, magnetic bit screening, and liquid penetrant screening.
Visual assessment is the most essential strategy, enabling the prompt identification of surface issues. Ultrasonic testing uses high-frequency audio waves to discover inner defects, while radiographic screening employs X-rays or gamma rays to imagine the inner structure of welds. Magnetic particle screening is reliable for spotting surface area and near-surface stoppages in ferromagnetic materials, and liquid penetrant screening discloses surface-breaking problems by applying a tinted color or fluorescent penetrant.
On the various other hand, destructive testing includes literally testing the welded joint up until failure to examine its mechanical homes. Devices such as tensile screening equipments, impact testers, and hardness testers are generally made use of in this context. By using a mix of these tools and techniques, inspectors can guarantee the high quality and security of bonded frameworks.
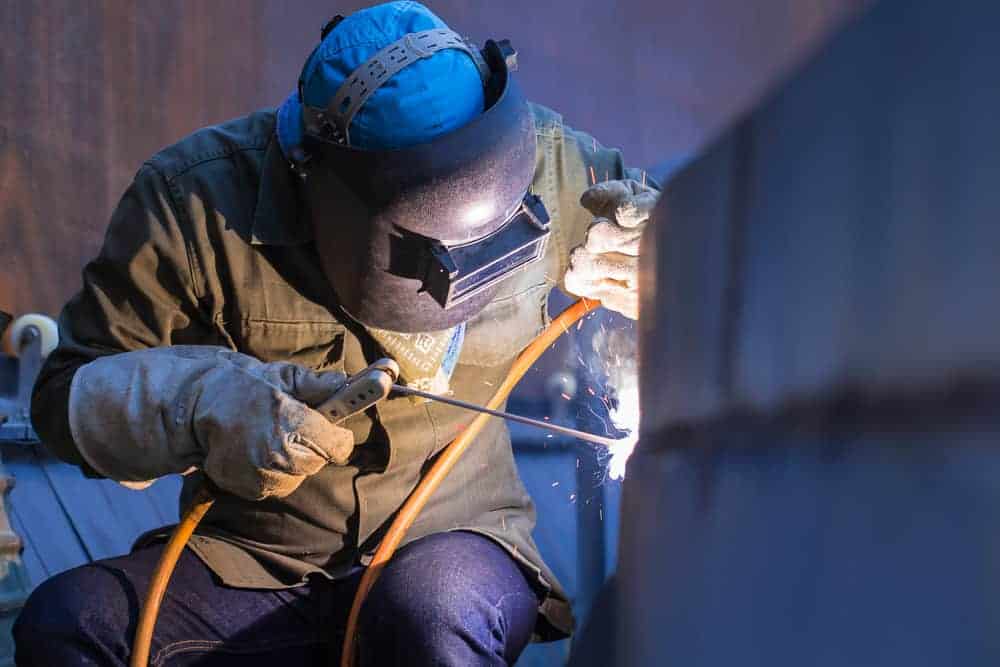
Relevance of Documents
In the realm of welding inspection, correct paperwork works as an essential backbone for quality guarantee and regulatory conformity. Paperwork encompasses a broad array of records, including weld procedure requirements, assessment reports, and non-destructive screening results. These documents not only supply a chronological account of the examination process yet also act as a reference for future analyses and audits.
Accurate documents guarantees that all welding tasks are proven and traceable, promoting adherence to relevant market criteria and codes. It becomes crucial during the evaluation procedure, allowing stakeholders to examine compliance with requirements and identify any type of inconsistencies or problems. Furthermore, thorough records support efficient interaction among team participants and exterior auditors, fostering a culture of transparency and responsibility.
Furthermore, properly maintained documents can significantly decrease the danger of expensive rework or failures. By making sure that all needed details is videotaped and easily accessible, organizations can improve their high quality guarantee procedures, eventually improving the stability you can try this out of the welded structures. For that reason, investing time and resources into creating durable documents techniques is not just a step-by-step demand however a tactical necessary for attaining long-lasting success in welding procedures.
Employee Certifications and Training
How can organizations make certain the proficiency of their welding workers? To maintain high criteria of quality control, it is essential for companies to invest in comprehensive training programs customized to the certain requirements of the welding sector. Welding Inspection Milwaukee. This includes not only preliminary training but additionally constant education to maintain personnel abreast of advancing techniques and innovations
Organizations should develop clear criteria for workers certifications, including relevant accreditations and experience in various welding methods. Using licensed welding assessors (CWIs) can enhance the top quality of evaluations, as these specialists possess the needed proficiency to recognize potential flaws and ensure adherence to best methods.
In enhancement to technological skills, organizations need to foster a culture of safety and security and conformity among their welding workers. Giving regular workshops and correspondence course can aid enhance the significance of security methods and the effects of non-compliance.
Furthermore, organizations must apply efficiency evaluations and feedback systems to examine workers expertise with time. By methodically addressing training basics needs and advertising a commitment to quality, companies can boost their welding assessment procedures, inevitably bring about boosted item honesty and consumer satisfaction.
Compliance With Industry Criteria
Following industry standards is paramount for ensuring the quality and safety and security of welding procedures. Conformity with well-known criteria, such as those established by the American Welding Culture (AWS), American National Requirement Institute (ANSI), and International Company for Standardization (ISO), supplies a framework for evaluating the integrity of welded frameworks. These requirements include various aspects of welding, consisting of product selection, design requirements, and step-by-step methods.
Welding inspections have to be performed based on these standards to validate that the work fulfills the see it here necessary high quality criteria. This consists of visual inspections, non-destructive screening (NDT), and extensive documentation of searchings for. Making sure compliance not just enhances the integrity of the welds however also alleviates risks linked with structural failings.
Additionally, adherence to industry requirements fosters a society of safety and expertise within the workforce. It develops a benchmark for efficiency and encourages constant improvement with normal audits and training. Eventually, conformity is not just a governing requirement; it is a dedication to quality that safeguards both employees and the environment while providing high-quality welding items.

Conclusion
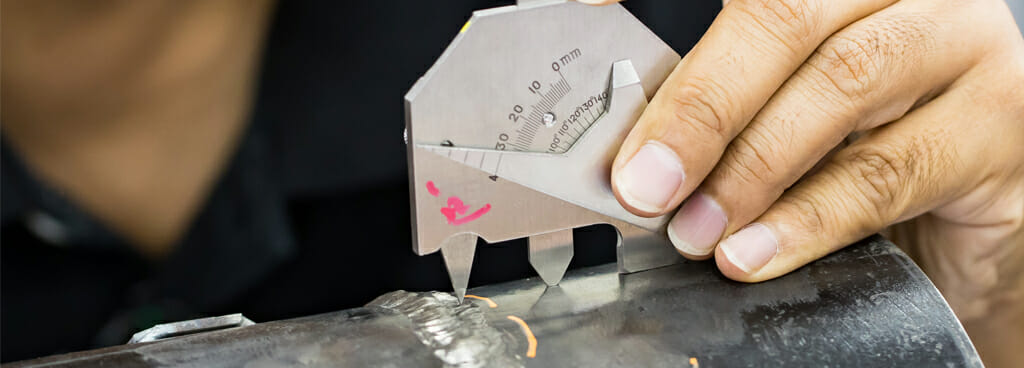
Welding examination is a vital aspect of high quality guarantee that encompasses different factors necessary for ensuring the stability of bonded structures.To make sure the honesty and reliability of welded joints, numerous inspection methods and devices are utilized throughout the welding process.In the realm of welding examination, proper paperwork offers as a critical backbone for high quality guarantee and governing compliance.Welding evaluations need to be performed in accordance with these standards to confirm that the job fulfills the needed quality criteria.In final thought, efficient welding examination for top quality guarantee requires a multifaceted method that includes the choice of proper assessment strategies, rigorous adherence to sector criteria, and comprehensive documentation of results.
Report this page